The universal encoder system U-ONE from Johannes Hübner Giessen combines speed, position and overspeed detection in a single unit. The system includes a universal basic unit that is connected to the electronic function modules on the switchboard via EMC proof fibre optic cable. Encased in a rugged aluminium casing, the basic unit UOM 4L-1212 is designed for maximum speeds up to 3000 rpm and the device is available as construction types B5 with flange and B35 with flange and foot.
Flexible Configuration
To facilitate flexible configuration of the U-ONE system it is possible to arrange the ten function modules that also belong to the system side-by-side in any order.
Combining up to ten functions, within one unit, the universal encoder system U-ONE, offers speed, position and overspeed detection diagnostics, without the requirement for additional units, resulting in a simplified and highly efficient solution for crane operators.
Current set-ups with separate sensing device units, all channelled through one gearbox, via separate cabling, raise issues with gearbox efficiency and when one unit fails, present potential problems with aligning replacements, correctly.
Connected to electronic function modules on the switchboard via EMC proof fibre optic cabling, the revolutionary U-ONE allows for effective detection and motion control functions, converting these readings and offering feedback to a central control device. The function modules can be flexibly configured as required, offering a number of possible activities to be carried out, in a pre-defined order. This, of course facilitates ongoing expansion of the modules and higher flexibility in planning future modifications.
Cost-Saving
This concept in engineering technology additionally offers considerable cost savings, thanks to its simple mechanical fitting, standardised electronic function modules, and reduced replacement and wiring requirements.
Speed and Position Monitoring
A relatively compact design and flexible configuration capabilities make the U-ONE a popular choice for monitoring speed and position – affording crane operators greater, more accurate supervision of the working processes. The supplementary electronic overspeed switch with a programmable switching speed from 0, offers additional control via the same switchboard mounted electronics.
Solutions to Suit You
The high degree of flexibility, in terms of functionality, order and development, makes the U-ONE an ideal solution for many crane operators; and coupled with the monetary savings on repairs and cabling and visually accessible display of services; provides a simplified, responsive device, ideally suited to the ports and harbours industry.
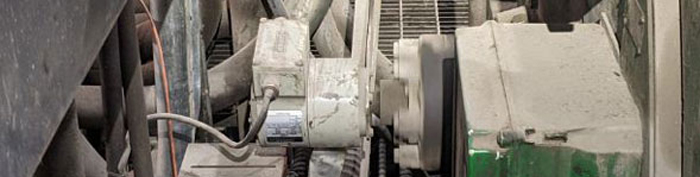
Case Study: Position monitoring on a coiler motor with functional safety
|
Rolling mills / coiler: safety-certified position monitoring on the coiler motor
- Several signal and switching outputs from one device
- Safe speed monitoring for direct integration into the safety chain
- Signal transmission via fibre optic cable
- Easy configuration of parameters for the electronic position and speed switches
The Task
The customer required a robust encoder for a coiler motor, the
transmission of the position signals via fibre optic cable, and
safety-certified speed monitoring.
The Solution
The customer was supplied with the robust
U-ONE universal encoder system with signal transmission via
fibre optic cable. The encoder system is designed for use in
heavy industry and offers high shock and vibration
resistance and a high degree of IP protection.
The modular design of the U-ONE encoder system provides
the customer with a tailor-made solution with transmission of
all required signals and contacts from one device. What’s more,
the system can also be extended at a later point in time without
requiring changes to the mechanical connection.
A complete solution has been provided, including a torque bracket and an adapter shaft.
Products
• U-ONE universal encoder system
• Adapter shaft
• Torque bracket |
|